New electronic controls have made their way into the Industrial Forklift Segment. The transistor now controls many Industrial Battery Chargers in the United States. While this technology has been proven in the European market for over 20 years, it only recently arrived in the U.S. a few years ago.
Today, there are four types of Industrial Battery Chargers: Ferro Resonant, Silicon-Controlled Rectifier (SCR), Hybrid, and the newer transistor-controlled High Frequency Chargers. Original equipment manufacturers (OEMs) typically produce at least one of these technologies, and some manufacture all four.
Each technology offers specific benefits in the industrial forklift segment, driving ongoing development and innovation. The Department of Energy has tested these technologies and is considering regulations that could potentially phase out older technologies in favor of newer, more efficient solutions.
In May 2009, Pacific Gas & Electric Company (PG&E) released a report comparing the energy usage, efficiency, and idle losses of these charger technologies. PG&E, a Northern California utility company, was commissioned by the Department of Energy to conduct and publish this study.
The full report is available online: www.energy.ca.gov. According to the data from the PG&E study, the new transistor-controlled technology saves 13% more energy compared to Ferro Resonant and SCR Technology. For a typical industrial electric forklift with a 40 kilowatt-hour battery, the energy savings can be substantial.
Most industrial customers pay an average of $0.15 per kilowatt-hour of electricity used. To determine true energy costs, divide the total monthly charge from the utility company by the total kilowatt-hours consumed, accounting for additional charges like demand fees, delivery costs, and taxes.
When recharging a 40 kilowatt-hour battery, the energy savings associated with different charger technologies can be seen in Table 1:

The PG&E study results suggest the energy savings shown in Table 1. Over the course of a year (312 operating days), this reduction in energy usage can translate into significant savings for the consumer.
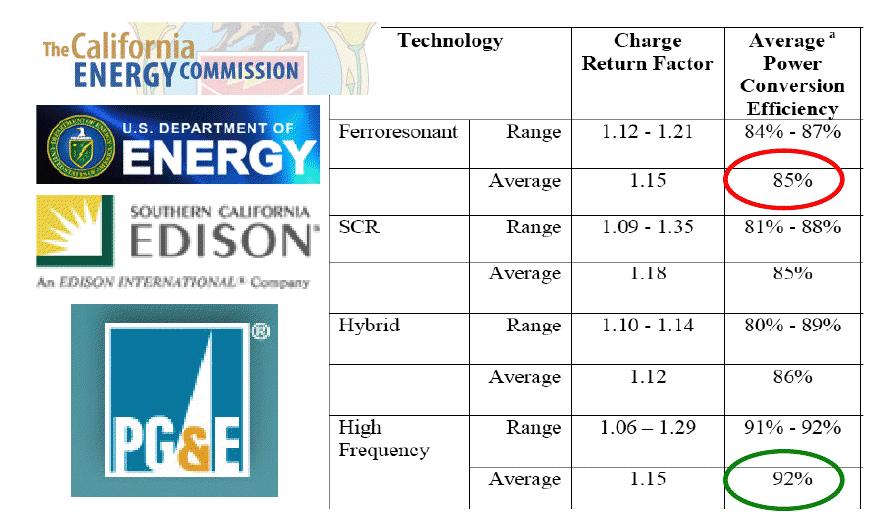

Table 2 shows that the energy savings per battery amounts to 2,028 kWh, or 13% of the total energy used. At a rate of $0.15 per kWh, this results in an annual savings of approximately $304 per battery. These savings should be taken into account when purchasing an Industrial Forklift Charger.
Cost differences between the technologies have narrowed, with the price difference averaging about 10%. The estimated costs for the chargers mentioned above are presented in Table 3:

In this example, the higher upfront cost of the transistor-controlled chargers is offset by the energy savings within less than a year. Due to this, the Department of Energy is considering mandating the use of Transistor-Controlled High Frequency Chargers in energy-sensitive areas like California, Nevada, and Arizona.
Additionally, transistor-controlled technology may offer further benefits, such as extending battery life. Many OEMs of High Frequency Chargers claim that these systems are “smarter,” utilizing more advanced algorithms for charging.
These advanced algorithms improve charge acceptance by lead-acid batteries, reducing chemical and heat stress during the charging process. As a result, batteries can achieve longer runtimes and extended overall lifespan.
Steve Munton is a nationally recognized expert in Energy, Sustainability, and Material Handling. He travels across North America, speaking on topics such as Energy Efficiency, Sustainability, the Triple Bottom Line, and Fossil Fuel Vehicle Usage in the Industrial sector.
Connect with Steve Munton on LinkedIn: www.linkedin.com/in/stevemunton