When most people think of forklifts, they picture the standard warehouse vehicle moving pallets around a distribution center. But in the diverse world of material handling, many industries face unique challenges that standard forklifts simply can’t handle. From freezing temperatures to explosive environments, specialized forklifts have evolved to meet these specific needs.
Today, let’s explore how these incredible machines have been adapted for some of the most demanding and specialized industries around the globe.
Cold Storage and Freezer Applications
Imagine working in temperatures as low as -30°C (-22°F). Standard equipment would fail within hours, but specialized cold storage forklifts keep the frozen food industry moving.
These cold warriors feature:
- Enclosed cabins with heating systems to protect operators
- Special hydraulic oils that maintain viscosity in extreme cold
- Sealed electrical components to prevent condensation damage
- Insulated battery compartments for electric models
- Non-slip features for icy surfaces
A frozen food distribution center might process thousands of pallets daily, and without these specialized machines, your favorite ice cream might never make it to the grocery store freezer.
Explosion-Proof Forklifts for Hazardous Environments
In chemical plants, refineries, and ammunition facilities, a single spark can spell disaster. That’s where explosion-proof forklifts come into play.
These safety-focused machines include:
- Sealed electrical systems that prevent spark generation
- Non-sparking materials for forks and other contact points
- Temperature-limited surface components
- Specialized exhaust systems (for combustion engines)
- Antistatic features throughout the design
These modifications come at a premium—often 2-3 times the cost of standard models—but are absolutely essential in environments where flammable gases, vapors, or combustible dust are present.
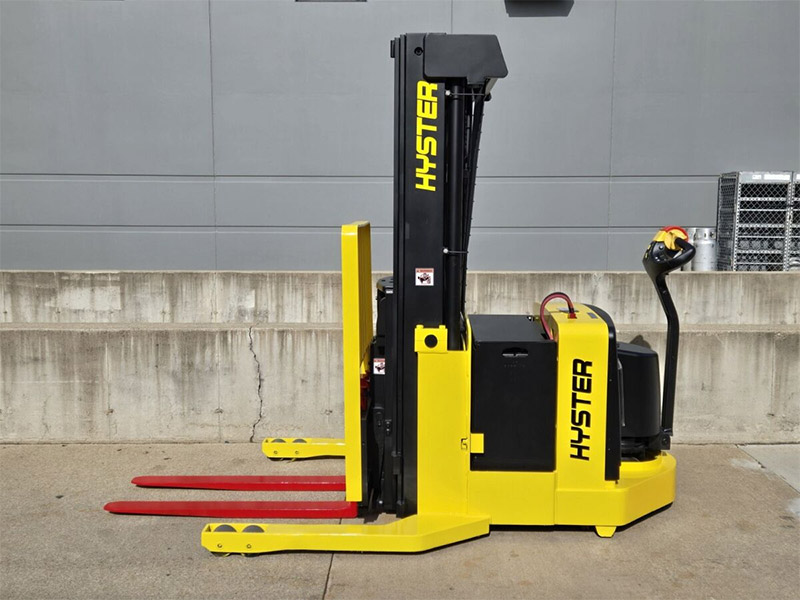
Narrow Aisle and Very Narrow Aisle (VNA) Forklifts
As real estate costs rise, warehouses are building upward and packing aisles closer together. Standard forklifts need about 12 feet to operate, but specialized narrow aisle forklifts work in spaces as tight as 8 feet, while VNA models can function in aisles just 5-6 feet wide.
These space-saving specialists feature:
- Articulating masts or forks for operating in confined spaces
- Wire or rail guidance systems for precise movement
- Reach mechanisms that extend forward or to the side
- Higher lift heights (often 40+ feet)
- Specialized operator controls for precision handling
One of my clients recently switched to a VNA configuration and increased their storage capacity by 42% in the same physical footprint—a game-changer for their expanding business.
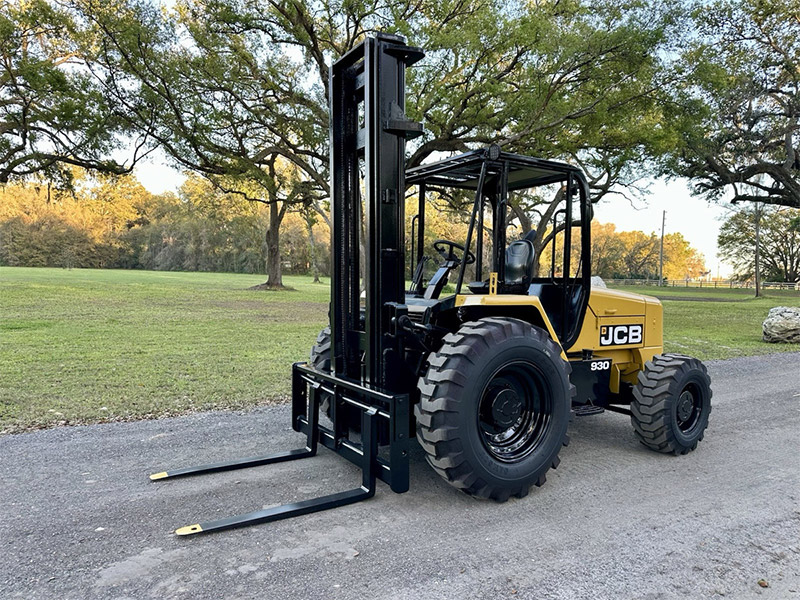
Rough Terrain Forklifts
Construction sites, lumber yards, and outdoor operations present challenges that would defeat a standard warehouse forklift in minutes. Rough terrain forklifts are the off-road vehicles of the material handling world.
These rugged machines boast:
- Large pneumatic tires with aggressive tread patterns
- Higher ground clearance for uneven surfaces
- Four-wheel drive capabilities
- Stabilizing outriggers for operation on slopes
- Weather-resistant components for outdoor operation
I once witnessed a rough terrain forklift deliver building materials up a 30% grade in pouring rain—something that would be impossible for its warehouse cousins.
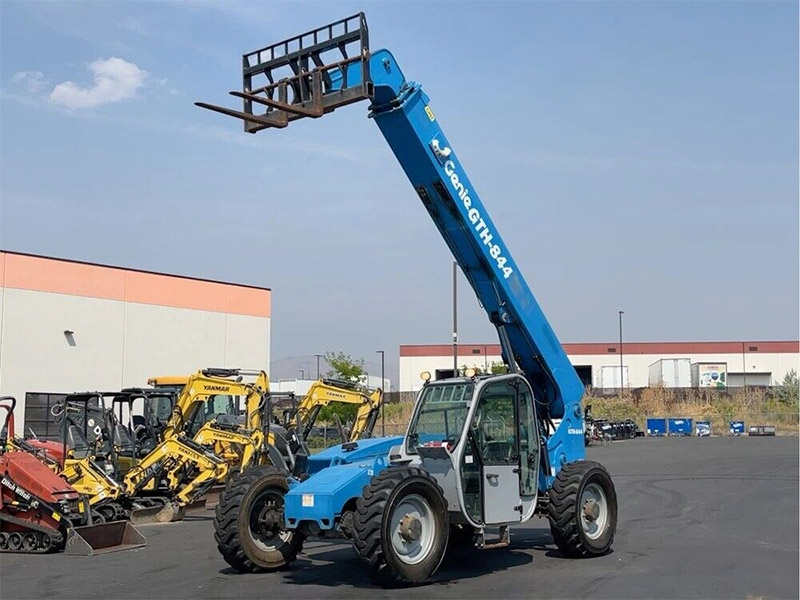
Telescopic Handlers (“Telehandlers”)
Combining the capabilities of a forklift with those of a crane, telehandlers feature a boom that can extend forward and upward, making them invaluable in agriculture and construction.
These versatile machines offer:
- Extended forward reach (up to 30+ feet)
- Lift heights exceeding 50 feet
- Quick-attach systems for different tools (not just forks)
- All-terrain capabilities
- 360-degree rotation in some models
A single telehandler can replace multiple pieces of equipment, making them a cost-effective choice despite their higher initial investment.
Side-Loading Forklifts
When handling long materials like pipes, lumber, or structural steel, traditional forklifts fall short. Side-loaders solve this problem by approaching loads from the side rather than the end.
These specialized machines include:
- Side-mounted forks or platforms
- Long load beds for material support
- Narrower profiles for operating in long goods storage areas
- Multi-directional movement capabilities
- Stabilization systems for handling unbalanced loads
Lumber yards particularly depend on these machines, as they can safely transport materials up to 40 feet long through narrow storage aisles.
Marina Forklifts
Waterfront operations present unique challenges, leading to the development of specialized marina forklifts for boat handling.
These waterfront workhorses feature:
- Corrosion-resistant components for saltwater environments
- Extended reach capabilities for boat storage racks
- Negative lift for launching boats below ground level
- Specialized attachments for hull support
- Higher weight capacities for larger vessels
These highly specialized machines can cost upwards of $300,000 but are essential for modern marina operations.
The Bottom Line: Specialization Drives Efficiency
While specialized forklifts come with higher price tags—sometimes 2-4 times the cost of standard models—they deliver tremendous value in the right application. The productivity gains, safety improvements, and capability enhancements often provide ROI within 18-24 months of deployment.
For businesses operating in unique environments, these specialized machines aren’t a luxury—they’re a necessity. As one warehouse manager told me, “We’re not paying more for a specialized forklift; we’re investing in the ability to do what standard equipment simply can’t.”